F1 News: VCARB CEO Reveals Issues Behind Mid-Season Performance Slump
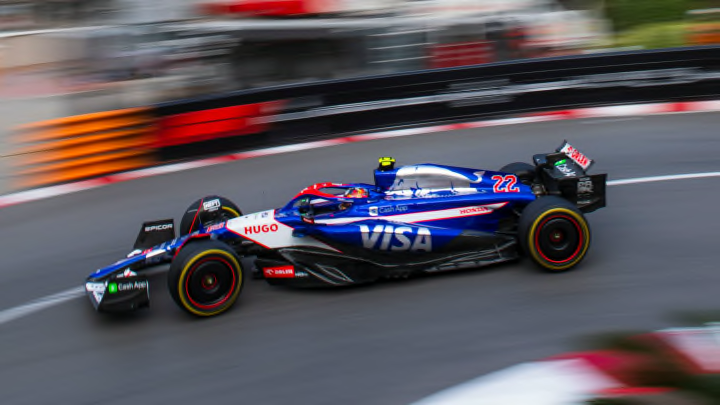
VCARB (RB) CEO Peter Bayer has elaborated on the 'slight correlation issue' that unexpectedly caused the fresh upgrades on the VCARB01 F1 car during the race weekend in Spain to perform as downgrades. However, through diligent investigation and patience, the team successfully pinpointed and addressed the root cause of the problem.
The issue arose following the introduction of upgrades for the Spanish Grand Prix, which included a new engine cover, rear wing, and updated floor. To the team's disappointment, this race unexpectedly saw both cars lacking pace with the poorest finish in the season thus far.
As it turned out, the upgrades didn't perform as expected, resulting in the cars finishing outside the points in P15 and P19, a stark contrast to their previous points-scoring races. Following thorough analysis, the team strategically reverted to a hybrid setup of old and new parts for the Austrian Grand Prix. Fortunately, this adjustment paid off as they successfully secured points in the race.
Having learned from the setbacks with the new parts earlier, VCARB made necessary adjustments and reintroduced them at Silverstone last weekend. This move paid off, resulting in a well-deserved points finish for the team, with Yuki Tsunoda securing the tenth place.
While there could have been several reasons for the drop in performance after the first upgrade, Bayer highlights the reasons for the team's setbacks and the steps it took to bounce back. He told PlanetF1.com:
“I think it was a couple of things.
“First of all, because it’s so tight, we’re obviously pushing as hard as we can to keep the edge.
“Now, to push as hard as you can, what does that mean? Well, it means that, in the design process, you’re pushing the guys to go to the limit and, in the factory, you go to the limit, meaning we run three shifts at the moment producing the parts. Three shifts mean 24 [hours].
“The pressure is as high off-track as it is on track. In that process, there were a couple of things as far as I understand."
He continued:
“There was a slight correlation issue with one of the aerodynamic parts. Because, ultimately, we’ve been very strong in slow corners, we’re not very good in terms of drag and efficiency so we tried to give up a bit of slow corner strength for high speed.
“And we did that. But, as we found out, we gave up a bit too much of slow-speed! So, once we understood that, we could go back.
“Then in terms of production, we had an issue with the rear wing, with a piece that was filled with aluminium. It turned out that aluminum was not strong enough to stand the load on the rear wing. It didn’t break, but it started to flop because it was not strong enough, ultimately.
“There was a small bit missing also on the wing, and, obviously, that could be fixed within a week and we had the new wing on the car [in Austria], where now the pieces are made of titanium and not of alloy, and it works.”