Nike utilizing innovative ridges for Olympic-ready soccer cleat

Cleat designers don’t often speak of peaks and valleys when discussing the outsole of their latest model, but Nike is doing just that for the launch of the Magista 2 in time for the Olympics in Rio and the fall start of European professional leagues.
While the Magista 2 has a showy neon “volt” yellow for its debut colorway, the cleat that Crystal Dunn and other U.S. women will wear comes in a red, white and blue design that matches seamlessly with the team’s Olympic uniform. Both are constructed from the now-signature Flyknit engineered yarn, but this cleat gets its shape from 3D printing.
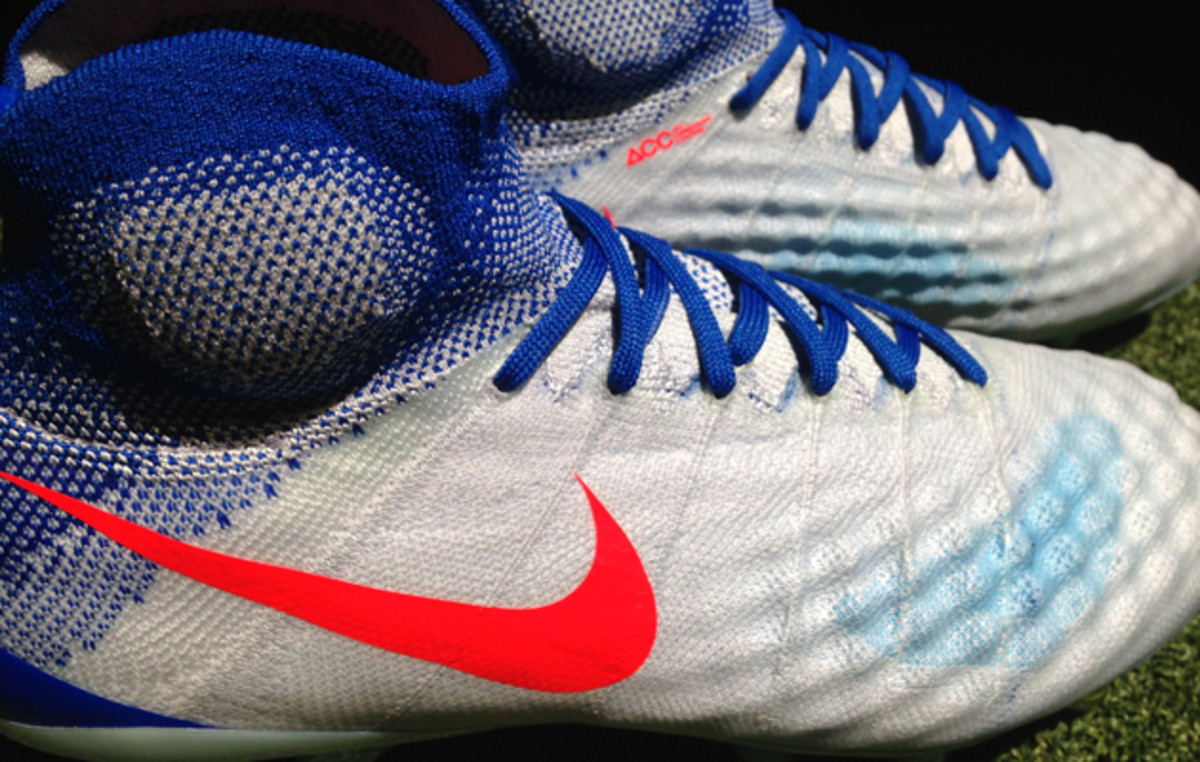
“The idea was to innovate around touch and grip,” Nate Van Hook, Nike soccer design director, tells SI.com. The "prune effect" fingers and feet experience when submerged in water for lengths of time helped define that design. Those small ridges that form on the extremities, Van Hook says, are actually a way improve grip when wet. That concept launched a hypothesis around soccer boot-to-ball grip that was put to 3D printers for “crude mockups,” which worked with peaks and valleys on the outsole.
• CREDITOR: Analyzing the U.S. women's roster for the Rio Olympics
“We started creating Frankenstein models,” Van Hook says. “We were seeing that instead of knitting (the grip), we were able to mold it.”
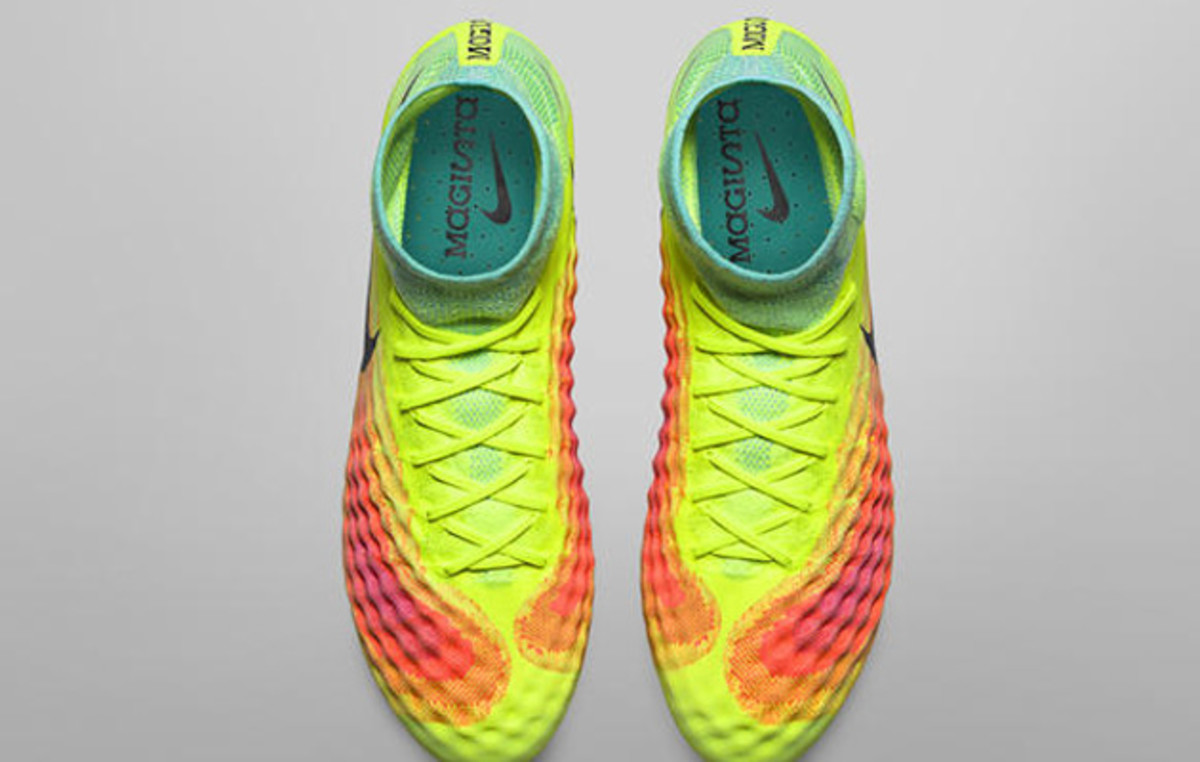
Van Hook and his team had to do a lot of tweaking to embroider the peaks and troughs at the proper height, one that allowed wearers to properly dampen the impact of the ball while also providing the right amount of feel. The ideal height ended up being 4.5 millimeters at its tallest point. Van Hook says they then went through 129 different Flyknit panels to build the Magista 2 with one continuous sheet of yarn. The final iteration—with much of the sensation data coming via player testing—comes with three different yarns, a supportive yarn on the heel and top of the foot, a structured yarn for the ridging and an elastic yarn for the molded, anatomical ankle cuff. “We were able to use a different yarn for different principles and tune every single area pixel by pixel,” he says.
The ankle cuff, which debuted on the Magista 1 takes on a new form in the cleat’s second version, with added padding to protect the heel and a fresh shape that cuts away material in the front and back to ease pressure on the foot and Achilles.
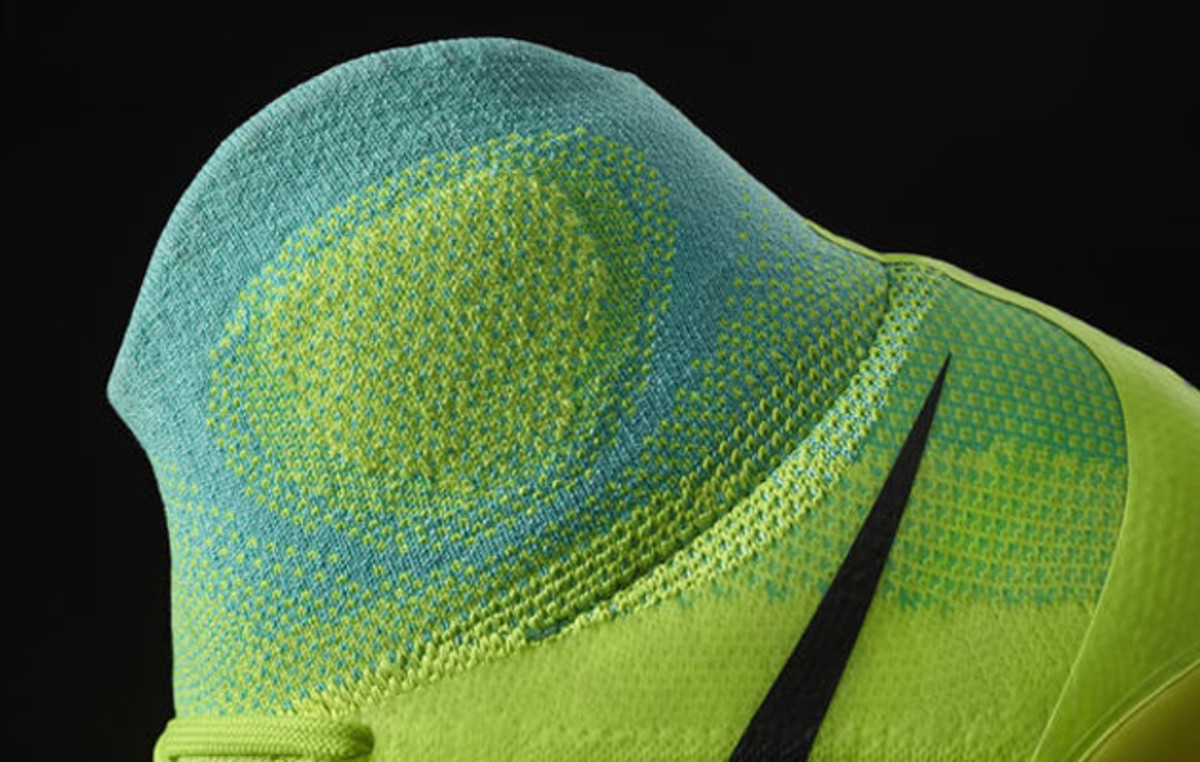
The outside of the cleat offers the ridges where lab testing showed it was needed based on ball striking data, but that carries to the inside too, where Van Hook says tiny nodes then interact with the foot. “When the ball comes in, areas dampen for great touch,” he says. “Inversely, the nodes go in and then the micro points interact with your foot.” He says the sensation helps players process the touch and feel of the ball.
• WAHL: Wide-ranging Q&A with the USWNT's Megan Rapinoe
The cleat, designed for midfielders and their need for control, meant Van Hook and designer Phil Woodman needed to rethink traction on the injection-molded cleat plate. Conical (round) studs have become common for allowing circular rotation, but by using 3D printing prototypes, the team determined it could create a more ground-locking stud with the same 360-degree movement by building a circular pattern of studs on the ball of the foot and have portions of studs shaved off.
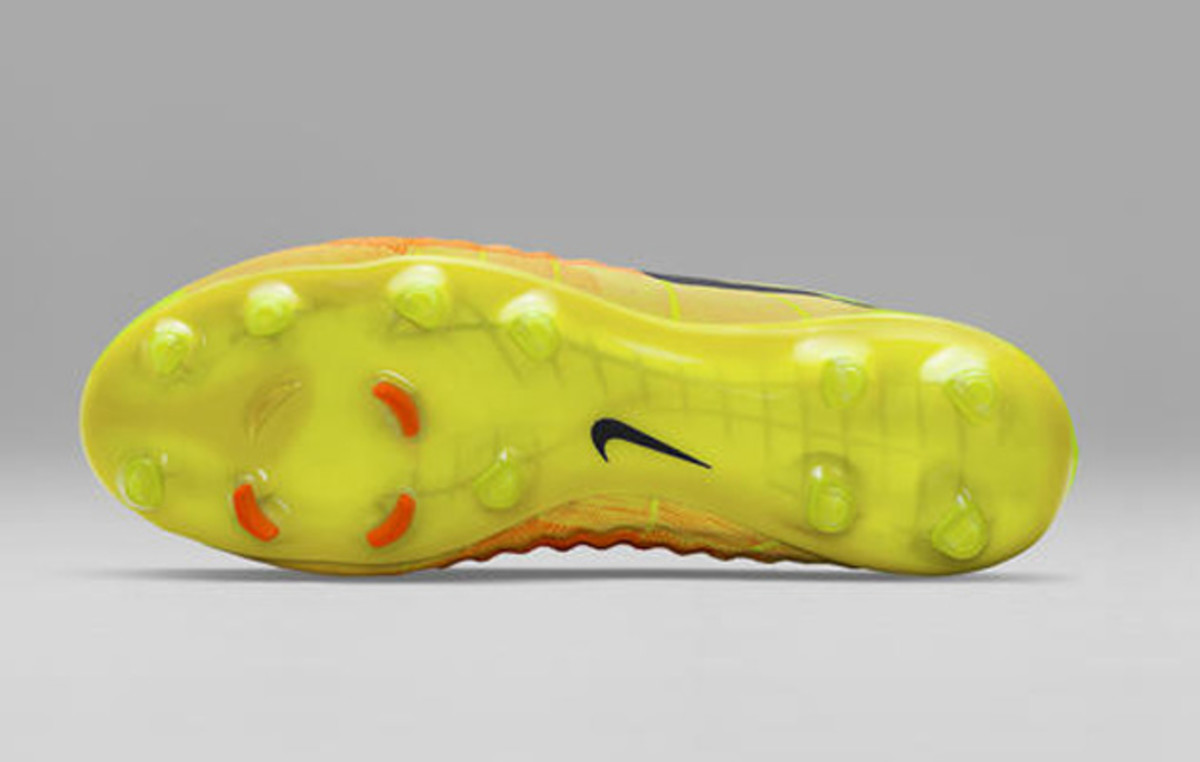
“We were able to take these studs and put them in a simulator and see how the traction is working,” Van Hook says.
Every step along the two-year path to create the Magista 2 used 3D molding and lab testing to keep the theory moving forward into product. But it all started with a prune-like finger.
Tim Newcomb covers sports aesthetics—stadiums to sneakers—and training for Sports Illustrated. Follow him on Twitter at @tdnewcomb.